Aluminum vs. Stainless in Marine Fabrication: Which Offers Better Corrosion Resistance?
In marine environments, where saltwater, humidity, and harsh conditions test materials daily, corrosion resistance isn’t a luxury - it’s a necessity. For boat builders, dock fabricators, coastal OEMs, and structural marine fabricators, the choice between marine-grade aluminum and stainless steel is critical to long-term performance, safety, and maintenance costs.
Both metals are widely used in marine fabrication, but their differences in corrosion resistance, strength, cost, and ease of fabrication make them better suited to specific applications. This article compares the two and helps you determine which material best fits your marine project needs.
Understanding Corrosion in Marine Environments
Marine environments pose one of the most aggressive corrosion challenges for metals. Saltwater contains high concentrations of chlorides, which attack unprotected metal surfaces, especially at welded joints, cut edges, or crevices where moisture can linger. Atmospheric marine environments, such as coastal cities or harbor facilities, also introduce salt spray and high humidity that can corrode even durable alloys over time.
To select the right material for marine fabrication, fabricators must consider both the type of exposure (fully submerged, splash zones, airborne salt) and the required lifespan of the equipment.
Comparing Marine-Grade Aluminum and Stainless Steel
Here is a side-by-side comparison of key characteristics:
Property | Marine-Grade Aluminum (5052, 5086, 6061, etc.) | Stainless Steel (304, 316) |
---|---|---|
Corrosion Resistance | Excellent in saltwater (especially 5052 & 5086) | 316 SS resists chlorides; 304 less so |
Weight | ~1/3 the weight of stainless steel | Heavier; adds stability but bulk |
Strength-to-Weight | High strength, especially in 5086/6061 | Stronger overall, but heavier |
Weldability | Easily weldable; minimal warping | Good weldability, especially 316 |
Cost | Generally more affordable | More expensive, especially 316 |
Maintenance | Low maintenance; doesn’t rust | 316 requires occasional cleaning |
Finish | Natural or anodized for protection | Polished finish resists fouling |
Applications | Hulls, docks, ladders, walkways | Railings, fittings, hardware, tanks |
Aluminum in Marine Fabrication
Marine-grade aluminum alloys like 5052, 5086, and 6061 are specifically engineered for harsh environments. These alloys resist corrosion naturally through the formation of an aluminum oxide layer, which acts as a protective barrier. When exposed to air and moisture, this layer continually renews itself, making aluminum self-passivating.
In applications like boat hulls, aluminum’s light weight helps improve fuel efficiency and handling. It also simplifies fabrication due to its ease of cutting, bending, and welding. Common marine structures such as floating docks, gangways, frames, and stairways rely heavily on aluminum due to its combination of corrosion resistance and strength-to-weight ratio.
For environments involving constant water contact or partial immersion, 5086 and 5052 offer superior pitting and crevice corrosion resistance. These alloys are often chosen for coastal walkways, barges, pontoons, and ferry components.
Stainless Steel in Marine Fabrication
Stainless steel offers unmatched strength, longevity, and a clean aesthetic, but not all grades are created equal for marine use. While 304 stainless steel is commonly used in commercial fabrication due to its excellent corrosion resistance in most environments, it is not recommended for chloride-rich marine conditions where pitting corrosion can quickly occur.
Instead, 316 stainless steel is the preferred grade for marine applications. Known as "marine-grade stainless," it contains 2-3% molybdenum, which enhances its resistance to chloride-induced corrosion. It holds up well in salt spray zones, deck fittings, exposed fasteners, and tanks that store brine or saltwater solutions.
316’s strength and resistance to corrosion make it a popular choice for:
- Boat railings and hardware
- Cleats and anchor systems
- Washdown stations
- Seawater tanks
- Piping and valves in coastal facilities
It’s especially useful in hygienic or high-contact environments like fishing vessels, seafood processing plants, and marine sanitation systems.
Considerations for Fabrication and Cost
In many marine fabrication jobs, both aluminum and stainless steel may be used on the same project depending on the specific part’s role and exposure level.
Fabrication with aluminum is often faster and less energy-intensive. It cuts more easily, generates less tool wear, and requires less preparation. It also avoids red rust and is less likely to crack or distort during welding.
Stainless steel fabrication, while more demanding in terms of cutting and welding, provides higher rigidity and surface durability. Parts made from 316 stainless often require less structural support due to its inherent strength. However, fabricators must take care to prevent contamination and preserve corrosion resistance—particularly when grinding or welding in mixed-metal environments.
From a cost standpoint, aluminum tends to be less expensive, both in raw material and in overall fabrication time. But the long-term value of 316 stainless comes from its durability, low maintenance, and superior performance in constant salt exposure.
Environmental and Structural Application Factors
If your marine fabrication work involves weight-sensitive designs like small vessels, floating platforms, or elevated walkways, aluminum’s light weight is a clear advantage. Its use reduces stress on supports and simplifies transportation and installation.
In structural applications where rigidity, fire resistance, or long-term mechanical strength is critical, stainless steel may be the better fit. For example, pier supports, food-processing tanks, and marine washdown stations benefit from stainless steel’s stiffness, chemical resistance, and sanitary properties.
Additionally, some projects require a material that provides a finished, high-end appearance such as luxury marine hardware or architectural features on docks. In these cases, polished 316 stainless steel offers a premium aesthetic and long-term shine, whereas aluminum may dull unless anodized or regularly maintained.
Corrosion Resistance in Practice
While both materials are corrosion-resistant, their behavior in real-world marine environments differs. Aluminum’s oxide layer offers excellent protection, but it can degrade in strongly acidic or alkaline environments, or in tight crevices where water cannot evaporate. For this reason, proper design and drainage are critical when using aluminum.
Stainless steel, particularly 316, resists both oxidation and chloride pitting, but it is not immune to corrosion. In stagnant saltwater, poor ventilation, or tight fittings where moisture lingers, even 316 can experience localized pitting or crevice corrosion if not properly cleaned and maintained.
The decision often comes down to the exact environment fully submerged? Intermittent splash? Salt spray zone? The answer helps determine which material will maintain integrity over time with minimal upkeep.
Material Selection Summary
To determine the best material for your marine fabrication project, evaluate three things: corrosion exposure, structural requirements, and budget. If you need lightweight components that resist corrosion with minimal cost, marine-grade aluminum may be the best option. If strength, appearance, and long-term durability in harsh conditions are more important, 316 stainless steel will deliver superior results.
In many applications, the best solution lies in using both metals strategically, for example, aluminum frames with stainless fasteners, or stainless tanks with aluminum platforms. Knowing when and where to apply each is key to getting the most out of both materials.
Supporting Coastal Fabricators with the Right Material
Sourcing the right grade, in the right form, and at the right time is essential to keeping marine fabrication projects on schedule and within spec. Whether you're building coastal structures, outfitting vessels, or fabricating food-grade components for use on the water, access to corrosion-resistant metal is critical.
Action Stainless stocks a full range of marine-grade aluminum alloys and 316 stainless steel sheet, plate, and bar, cut to your exact specs. With value-added services like precision sawing, shearing, and CNC processing, we help fabricators reduce waste, increase output, and deliver projects that perform reliably in corrosive environments.
Ready to tackle your next marine fabrication project?
Let Action Stainless help you select and process the right material for long-term performance in coastal or saltwater environments.
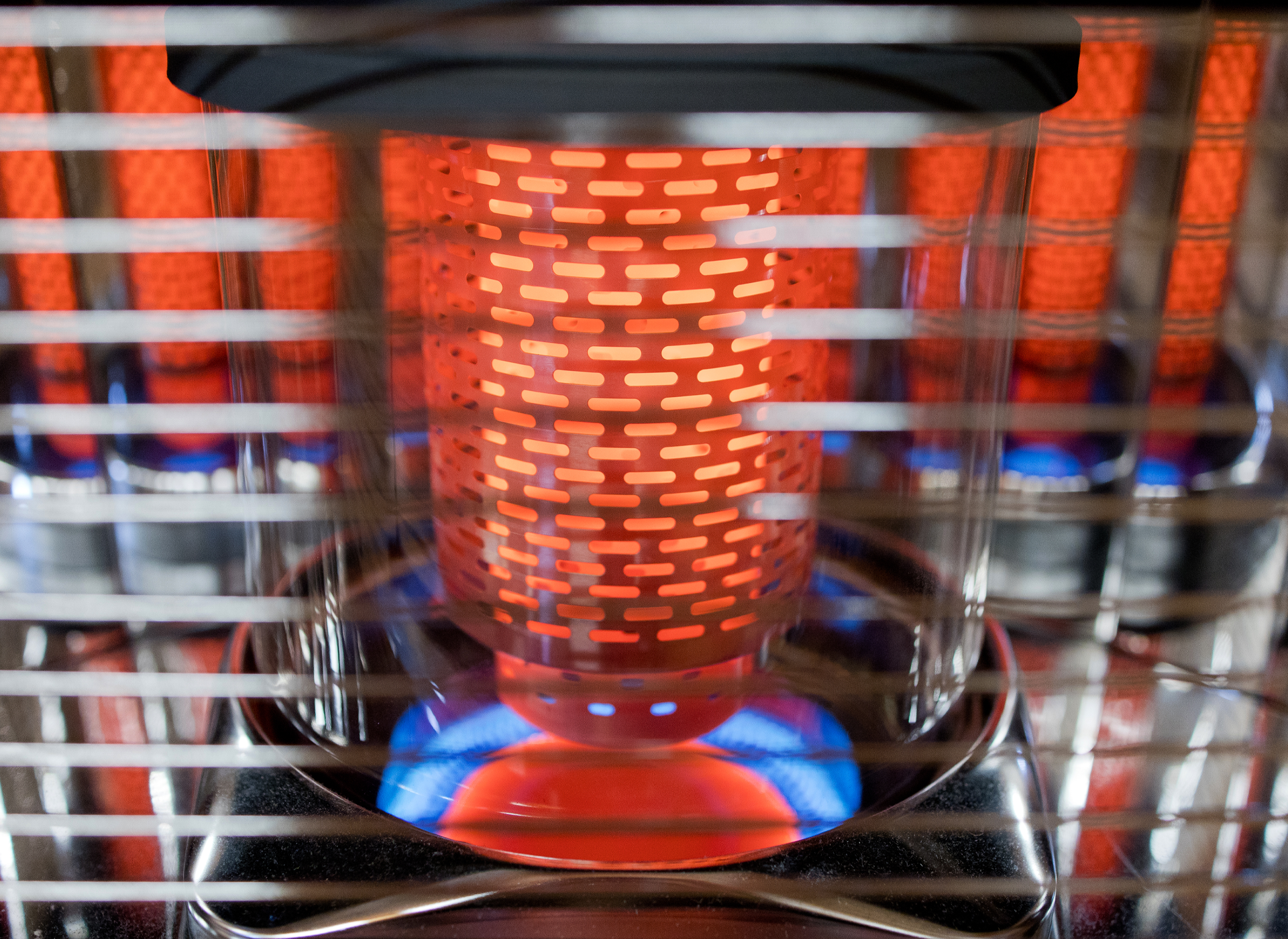