Key Differences Between 6061-T6 and 5052-H32 in Structural Aluminum Projects
When designing and fabricating structural components in demanding environments, material selection is critical. Two of the most widely used aluminum alloys in this category 6061-T6 and 5052-H32 offer distinct mechanical properties, strengths, and application benefits. Choosing the right one can improve performance, reduce costs, and extend product life.
Action Stainless supplies both grades at volume, and many customers across construction, transportation, and marine industries ask: Which alloy is better for structural aluminum projects - 6061 or 5052?
Understanding the Basics: 6061-T6 and 5052-H32
Both 6061-T6 and 5052-H32 are part of the 5xxx and 6xxx aluminum series, respectively, but they differ in composition, hardening method, and structural capacity. Here's how:
Property | 6061-T6 Aluminum | 5052-H32 Aluminum |
---|---|---|
Series | 6xxx (Al-Mg-Si) | 5xxx (Al-Mg) |
Temper | T6 (solution heat-treated and aged) | H32 (strain-hardened and stabilized) |
Yield Strength | ~35,000 psi | ~28,000 psi |
Ultimate Tensile Strength | ~45,000 psi | ~38,000 psi |
Formability | Moderate | Excellent |
Weldability | Good (post-weld strength drops) | Excellent |
Corrosion Resistance | Good | Superior |
Machinability | Good | Fair |
Common Applications | Structural frames, truck parts, bridges | Tanks, enclosures, marine fittings |
Mechanical Strength and Load Capacity
If strength and stiffness are the priority,
6061-T6 is the superior choice. With higher yield and tensile strength, it performs better in structural beams, supports, and welded framework where load-bearing performance is non-negotiable.
That said, its post-weld strength can decrease significantly, which needs to be factored into final engineering decisions. Designers often account for this by overbuilding the welded zones or performing post-weld heat treatment.
5052-H32, while slightly lower in overall strength, remains durable enough for many structures that also require flexibility, especially curved or formed profiles. It also offers better resistance to fatigue and vibration, making it popular in dynamic marine environments.
Formability and Fabrication Ease
5052-H32 is highly formable without cracking, making it ideal for projects involving:
- Radius bends
- Curved structural shapes
- Cold forming
This gives it an edge for applications where contouring is needed such as architectural panels, boat hulls, or bulkheads.
6061-T6 has lower elongation before breakage and can crack during tight bends unless it’s annealed first. It is better suited for projects where precise machining and straight-line fabrication dominate the process.
Corrosion Resistance in Harsh Environments
5052-H32 is naturally more corrosion-resistant, especially in saltwater and acidic environments. Its high magnesium content (2.2–2.8%) makes it a preferred alloy in:
- Marine structures
- Salt-air coastal architecture
- Chemical storage tanks
6061-T6 performs well in most environments but can be susceptible to galvanic corrosion, especially in marine conditions. When structural strength is required in corrosive areas, protective coatings or anodizing are often applied to extend the material’s life.
Weldability and Post-Weld Strength
Both alloys weld well using standard TIG or MIG processes. However, 5052-H32 maintains its strength better after welding without requiring post-processing.
6061-T6, on the other hand, loses strength in the heat-affected zone unless the part is re-heat-treated after welding. For critical welded structures, this adds cost and complexity but yields a stronger final assembly.
Machining and Finishing
6061-T6 is widely recognized for excellent machinability. It produces clean chips and accepts tight tolerances, making it ideal for parts requiring drilled holes, tapped threads, or complex geometries.
5052-H32 machines adequately but is softer and more prone to galling. For projects requiring extensive milling, threading, or tapping, 6061 offers more reliability and cost efficiency.
Which Alloy Should You Choose?
Your choice depends on the specific goals of the project. Here's how it breaks down by typical application priorities:
- High Strength, Machining, Straight Lines → 6061-T6
- Formability, Marine Resistance, Complex Shapes → 5052-H32
- Welded Structures with No Heat Treatment → 5052-H32
- Anodized Parts or Post-Weld Machining → 6061-T6
Applications in Structural Fabrication
6061-T6 is often used for:
- Structural supports and framing systems
- Vehicle chassis and trailer frames
- Ladder systems, platforms, and truck beds
- Aerospace brackets
5052-H32 is commonly used for:
- Marine walkways and staircases
- Storage tanks and containers
- Building panels in coastal areas
- Railing systems
Working with Action Stainless on Aluminum Stock
Action Stainless stocks both 6061 and 5052 in various thicknesses, sheet sizes, and bar shapes. Whether you’re sourcing for heavy-duty truck frames or designing corrosion-resistant enclosures, our team ensures timely delivery and cut-to-size services to meet your exact fabrication needs.
We support clients in industries ranging from marine and construction to chemical and commercial transportation, and we provide aluminum products ready for laser, plasma, and waterjet cutting.
Conclusion
6061-T6 and 5052-H32 both offer distinct benefits for structural aluminum projects. The choice ultimately depends on your balance between strength, corrosion resistance, and fabrication needs. For heavy structural loads and precise machining, 6061-T6 is ideal. For superior corrosion resistance and easy forming, 5052-H32 excels especially in marine and chemical environments.
Action Stainless is here to help with both. From raw sheet and plate to custom-cut profiles, we’re committed to supporting your aluminum fabrication success.
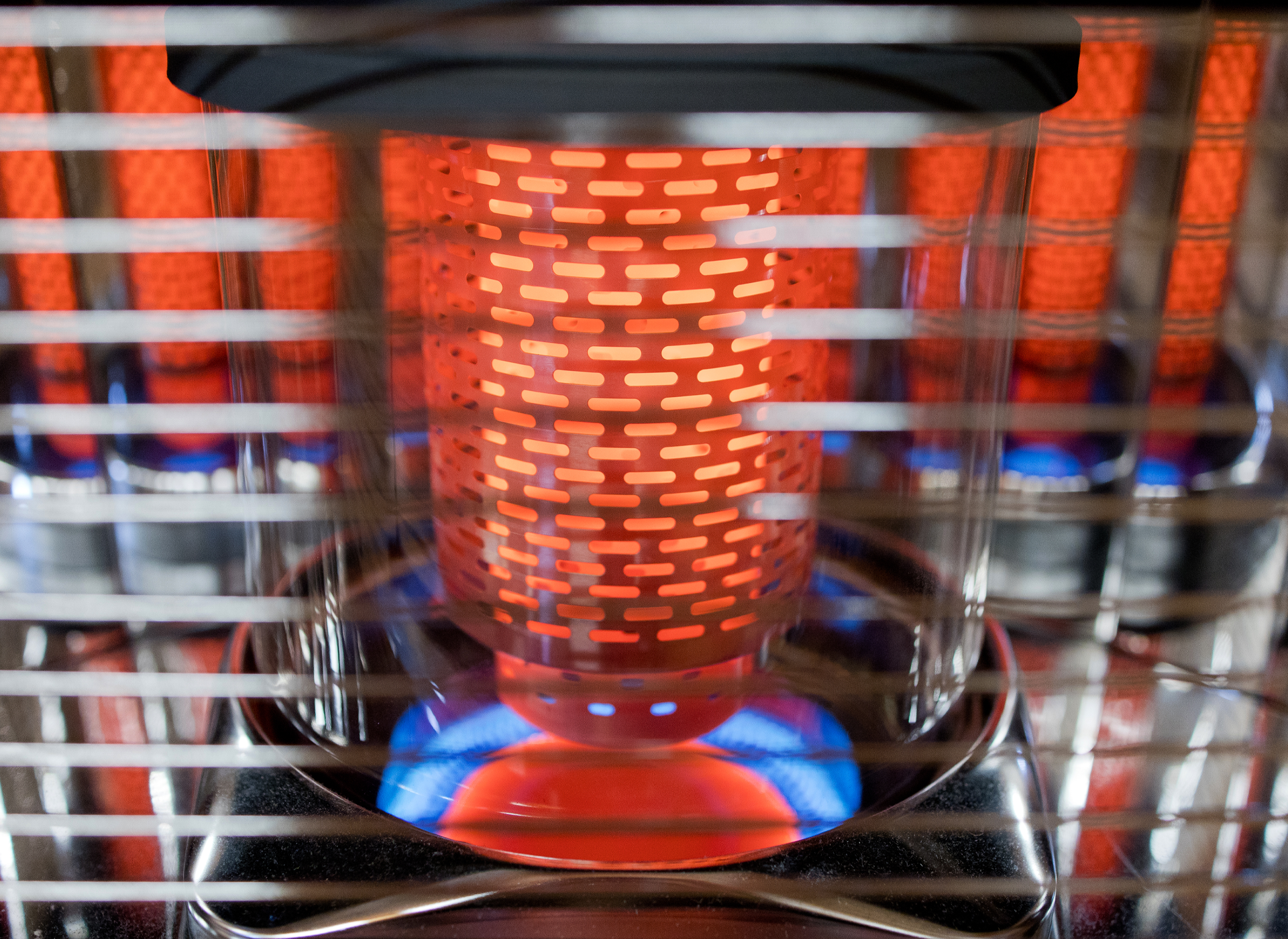