Common Mistakes to Avoid When Selecting Aluminum Alloys for Projects
When working with aluminum for fabrication projects, choosing the right alloy is one of the most critical decisions. Aluminum’s lightweight strength and corrosion resistance make it ideal for a wide range of industries, from food processing and signage to marine components and structural framing. But with multiple grades available, each offering different properties, it’s easy to make costly mistakes that can impact performance, durability, or fabrication efficiency.
At Action Stainless, we stock and process the most widely used aluminum grades in fabrication: 1100, 3003, 6061, and help customers across industries choose the best match for their needs. This guide highlights common mistakes to avoid when selecting aluminum and explains how to ensure your alloy choice supports your application, budget, and project timeline.
Understanding Aluminum Grades: A Quick Overview
Before diving into what can go wrong, it helps to understand what each commonly used grade offers:
- 1100 Aluminum: A commercially pure aluminum (99%+), known for excellent corrosion resistance, workability, and thermal conductivity. Non-heat treatable and softer than other grades.
- 3003 Aluminum: An aluminum-manganese alloy with better strength than 1100 while retaining good corrosion resistance and formability.
- 6061 Aluminum: A heat-treatable aluminum-magnesium-silicon alloy offering high strength, corrosion resistance, and weldability. Suitable for structural applications.
Each grade brings unique value but also potential drawbacks if used in the wrong application.
Mistake #1: Choosing Based on Strength Alone
A common error is selecting aluminum solely for its strength, without considering other key factors like formability or corrosion resistance. For instance, 6061 is much stronger than 1100 or 3003, but that added strength can make it harder to bend or form. If your part requires tight bends or deep drawing, a softer grade like 3003 may be the better option.
What to do instead: Evaluate not only the required mechanical strength but also how the part will be fabricated. Will it be stamped, bent, or spun? Do you need it to hold up under impact or flex without cracking?
Mistake #2: Overlooking Weldability and Joint Quality
Not all aluminum grades weld the same way. Using a grade with poor weld characteristics can weaken the joint or require additional filler metals.
- 1100 offers excellent weldability but lower structural strength.
- 3003 is easily welded and holds up better than 1100 in moderate strength applications.
- 6061 is weldable, but without post-weld heat treatment, the heat-affected zone (HAZ) can be significantly weaker.
Tip from Action Stainless: For applications requiring welding, be sure to match the alloy with proper filler metals and, if needed, plan for heat treatment or strengthening processes after welding.
Mistake #3: Ignoring Corrosion Resistance in Service Environments
Using an alloy that isn’t suited for your environment can lead to premature failure. For instance, 6061 performs well in general atmospheric corrosion but is not the best option in saltwater or marine settings, where 1100 or marine-specific alloys may perform better.
- 1100 is highly corrosion-resistant and often used in food and marine applications.
- 3003 is slightly less corrosion-resistant than 1100 but still performs well.
- 6061 is generally good but vulnerable in some aggressive chemical or marine settings.
Use Case Example: A mistake would be choosing 6061 for an exterior food processing guard in a high-humidity room when 3003 or 1100 would hold up better without surface treatment.
Mistake #4: Not Considering Finish Requirements
Finish quality matters, especially for consumer-facing or architectural components. 1100 and 3003 both offer excellent surface appearance and polish well, while 6061 may require more finishing to achieve the same effect.
If the application demands a high-polish or decorative finish, using 6061 might require extra work, cost, or compromise the look of the product.
Better choice: Use 1100 or 3003 for signage, food service trays, or decorative trim where finish is a high priority.
Mistake #5: Selecting an Alloy Without Considering Machinability
Machinability varies significantly by grade. If your parts need to be milled, drilled, or turned to tight tolerances, using a grade that gums up tools or creates inconsistent finishes can delay production.
- 6061 is known for excellent machinability among aluminum grades.
- 1100 is soft and tends to gum tools, requiring slower speeds and careful technique.
- 3003 is moderate, better than 1100 but not ideal for precision machining.
Action Stainless Tip: For CNC machining or parts requiring fine threads, 6061 is often the preferred choice.
Mistake #6: Ordering the Wrong Thickness or Temper
Each aluminum grade is available in multiple tempers (like H14 or T6) and thicknesses. Choosing the wrong one for the forming method or structural load can lead to cracking, warping, or failure under stress.
For example, using 6061-T6 where a softer temper is needed for bending could lead to fractures. Similarly, using a thin-gauge 1100 in a structural bracket might cause deflection.
Best Practice: Confirm temper and thickness with your fabrication team and consult Action Stainless for available stock that fits your application.
Grade Comparison Table
Property | 1100 | 3003 | 6061 |
---|---|---|---|
Strength | Low | Medium | High |
Corrosion Resistance | Excellent | Good | Good |
Formability | Excellent | Good | Fair |
Weldability | Excellent | Excellent | Good (needs care) |
Machinability | Low | Moderate | Excellent |
Polishing/Finish Quality | High | High | Moderate |
Mistake #7: Not Verifying Material Certifications
Industrial projects often require material certifications for traceability and compliance. Ordering aluminum without verifying whether mill test reports (MTRs) are included can create issues during inspections or downstream processes.
Our standard at Action Stainless: We provide MTRs with all aluminum orders upon request and ensure that all material complies with ASTM and relevant industry specifications.
Mistake #8: Underestimating the Role of Cutting Method
As we've covered in our aluminum cutting blogs, the choice between waterjet and saw cutting matters when working with aluminum. Softer alloys like 1100 may deform or burr during aggressive saw cutting, while 6061 handles it better.
Waterjet cutting is often the best method for precision parts or when minimizing heat and distortion is critical.
Cutting Tip: Always match your alloy and geometry with the right cutting method. Our team can guide you on how best to cut and form aluminum parts to spec.
Mistake #9: Over-Specifying for Basic Applications
Sometimes, engineers or buyers choose higher-cost alloys like 6061 when a simpler, more cost-effective alloy like 3003 would do the job just as well. Over-specifying can inflate budgets without adding value.
Action Stainless Approach: We work closely with clients to assess application needs and recommend the most cost-effective, compliant alloy based on environment, strength, and fabrication method.
Industries That Rely on Action Stainless Aluminum Grades
We supply cut-to-length aluminum in 1100, 3003, and 6061 for industries such as:
- Food Processing: Sanitary trays, machine guards, and enclosures
- Marine Fabrication: Lightweight, corrosion-resistant panels and brackets
- OEM Equipment: Frames, housings, access panels
- Architectural: Trim, decorative panels, signage
- HVAC: Panels, ductwork, support brackets
Get the Right Aluminum for Your Next Project
Avoiding these common aluminum selection mistakes can improve the performance, durability, and cost-effectiveness of your fabricated parts. Whether you're selecting 1100 for food-safe trays or 6061 for structural brackets, our team at Action Stainless is here to guide you from material selection through cutting, forming, and delivery.
Need help choosing the right aluminum grade?
Contact Action Stainless to request a quote or explore our in-stock aluminum materials, processing services, and expertise in aluminum fabrication.
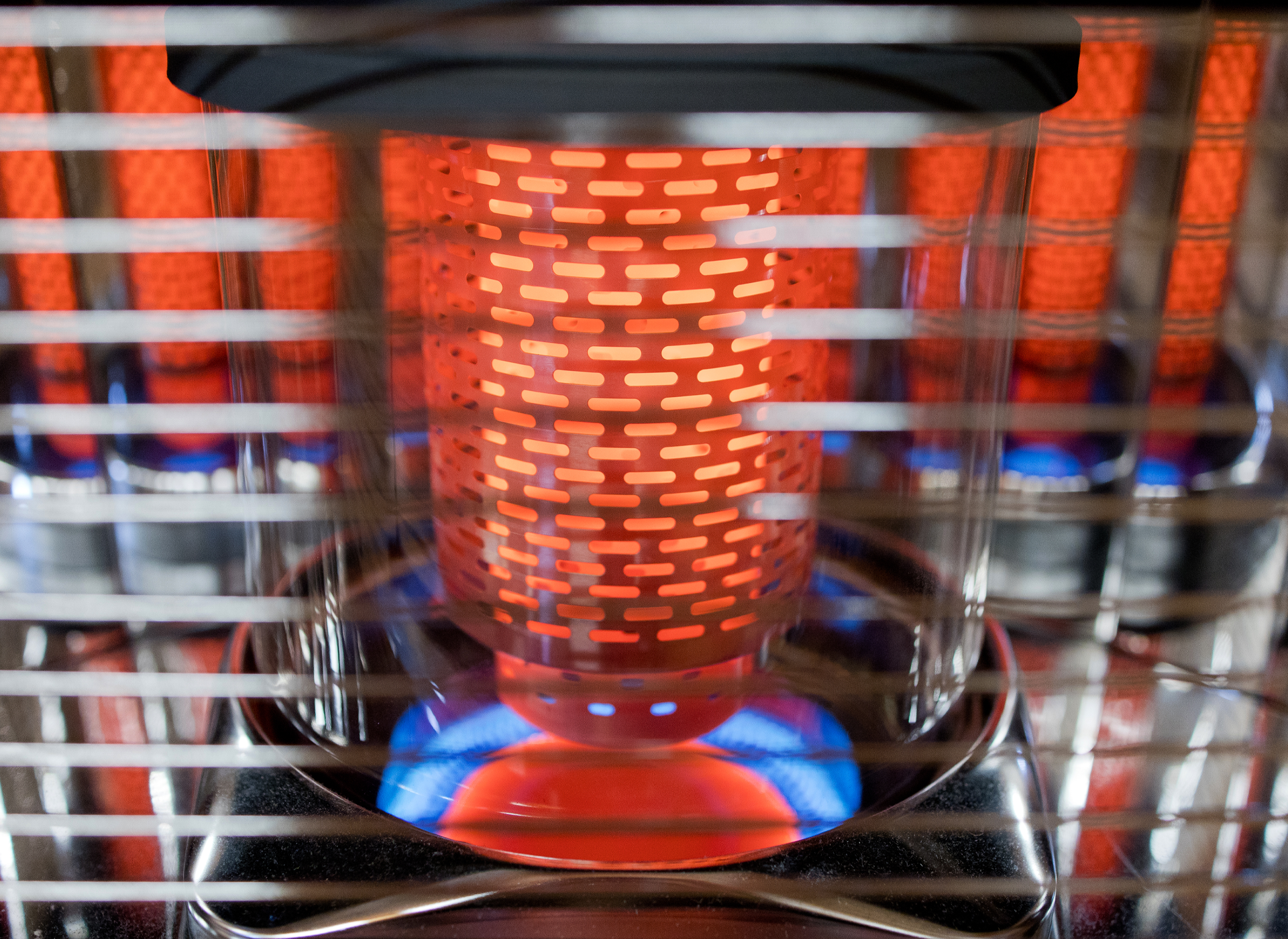